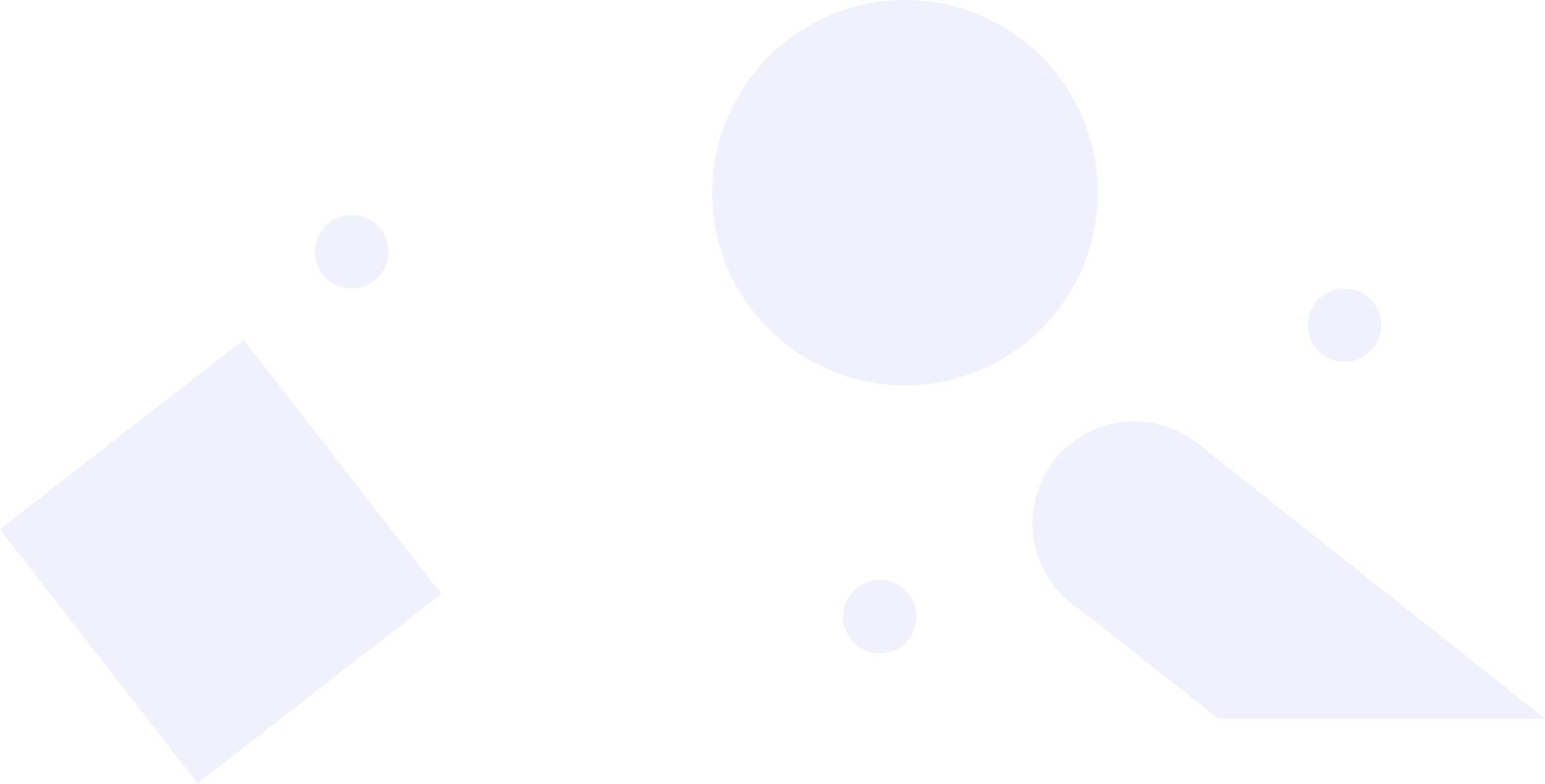
Optimal Design of Composite Structures Overview
Partnering with the US Navy and composite manufacturing industry leaders, one of the principals leveraged a Pareto optimization approach to determine the optimal separation displacements in the cohesive bond between the fiber and matrix material of a dynamically loaded unidirectional composite to arrest a projectile with the least amount of material damage. The optimal design parameters were determined using a genetic algorithm inspired technique called GANBI by approximating the Pareto front for the competing objectives of minimizing material damage while maximizing the cohesive failure.
Client’s Modeling and Design Impact
The client gained a multiobjective design framework that takes the designer out-of-the-loop and determines the optimal set of values for the design parameters which are chosen a priori. The framework approximates the Pareto front and therefore the set of optimal designs for competing objectives in unidirectional composite panel design subjected to projectile impact.
The approach drastically decreased the client’s computational burden on a as the Pareto front was determined in only 24 simulations (~384 hours) over the conventional build-test-build approach which would require 3 to 4 times as many simulations (~1536 hours). Furthermore, this allowed the client to decrease the time between numerical simulations and composite panel manufacturing and as a result minimized overall manufacturing material resources and cost which maximized product design efficiency and profitability.
Fiber-reinforced Composite Design Challenges
Fiber-reinforced composites such as unidirectional composites offer an advantage over conventional materials due to their tailorability. A designer has a suite of potential design variables to adjust in order to meet specific design goals and requirements. Furthermore, the designer might not realize the full potential of the composite if the optimal set of design variables is not chosen. Customizable design variables include fiber and matrix materials (e.g., elastic, plastic, viscoelastic, high strain rate, etc.), lamina architecture, failure mechanisms (e.g., cohesive/adhesion failure, matrix cracking, fiber breakage, fracture, etc.), and laminate stacking schedules and orientations. These variables are chosen in order to satisfy specific design goals such as: minimize cost, weight, buckling and/or maximize strength, energy absorption, resonance frequency, and stiffness in a certain direction.
The large number of design variables makes determining the optimal design of fiber-reinforced composites a very complex problem. Complexities in the design of fiber-reinforced composites are manifested in two ways: (1) optimal designs could be problematic to obtain due to the high dimension and existences of parameter dependencies/coupling in the design space and (2) modeling challenges due to capturing intricate geometries, failure conditions, and loading/boundary conditions. It is infeasible from a computational resource and management perspective to fully explore the design space to determine the optimal set of designs.
Cohesive Zone Modeling for Energy Dissipation
It is commonly the goal of a designer or manufacturer to design fiber-reinforced composites such that the cohesive bonds between the fiber and matrix interface fail before the fiber or matrix material fails. The energy that it takes to fail this bond is a primary energy dissipation pathway for the composite. When the bond fails, the fiber and matrix materials are still intact and can therefore still support the load—whose energy has been dissipated by the bond failures. However, if the materials fail, the composite can no longer support a load. In the composite model presented here, we will consider material (fiber and matrix) failure and cohesive (fiber-matrix interfacial) failure. Cohesive failure is modeled as a two-step procedure. First, a maximum separation-based linear damage initiation law is used. Once a specified threshold value is met for damage initiation, a displacement-based linear damage evolution law is used.
Unidirectional Composite Model
A quarter-symmetric (0/90) UD fibrous composite laminate subjected to an impact by a fragment simulating projectile was developed and simulated using ABAQUS/Explicit. The fiber and matrix material were all modeled with quad elements (ABAQUS type Q4). Quarter-symmetric representations were permissible provided that the material properties, displacement boundary conditions, and applied loads were collectively quarter-symmetric. In Fig. 1, the quarter-symmetry planes are the YZ- and YX-planes. The boundary conditions were such that no translations normal to the planes were admissible.
Figure 1: Left: Surface view of the two-ply model of the polymer matrix (green) and the UHMWPE fibers (red); Right: Subset view of the model depicting the mesh detail adjacent of two fibers
General contact surfaces and surface interactions (hard overpressure) were established between the matrix and fibers and between the fibers with each other. A nominal coefficient of friction, μ = 0.1, was used between the fibers, matrix, and fragment simulating projectile (FSP) materials. This necessary condition restricts the fibers from occupying the same space once the matrix elements have failed. The fibers can still come in contact but cannot cross into each other. For the ballistic impact case, contact was defined for the matrix and FSP as well as the fibers and FSP. It was necessary to establish contact between the fibers and FSP because, as the matrix material degraded due to failure, the FSP came into contact with the fibers. If fiber- to-FSP contact was not established, the FSP would simply pass through the fibers.
To simulate a ballistic impact event, a quarter-symmetric representation of a non-deformable FSP was used. The FSP and composite laminate is shown in Fig. 2 at the start of the simulation before the FSP contacts the composite. The FSP was composed of steel and modeled using six-node linear triangular prism continuum elements (ABAQUS type C3D6). A reference node on the FSP was driven by an initial velocity.
Figure 2: The FSP just prior to impacting the composite laminate
The Genetic Algorithm Normal Boundary Intersection (GANBI) Method
The GANBI method is based on the concept of building up an approximate Pareto surface by pushing out a coarse approximation of the convex hull of individual minima as far as possible at regularly spaced intervals while staying within the constraints of the design space. The design space that was considered was the displacements (damage initiation and evolution) in the traction vs separation failure laws for the cohesive failure which is depicted in Fig. 3. An initial assumption is the designer has determined (either through experience or through some optimal design means) the fiber and matrix materials to use.
Figure 3: Design space for the displacements in the traction vs. separation cohesive failure
The range of damage initiation displacements where chosen such that they are physically equivalent to the fiber displacing up to 18% of its diameter before damage has fully set in and the bond starts to break. The range of damage evolution displacements where chosen such that they are physically equivalent to the fiber displacing up to 71% of its diameter before the bond completely fails and releases energy. At this value, the fiber is almost in the same starting area of its neighboring fiber. The initiation displacement dependence on the minimum distance acts as a threshold just higher than that of the initiation displacement. These displacements are graphically illustrated in Fig. 4 where the original location of the fiber (black circle) is displacement to its maximum (blue circle) at the initiation point and then to its maximum (red circle) at the evolution point.
Figure 4: Graphical representation of the fiber separation for both damage initiation (blue)
Optimal Parameter Determination in Composite Panel Design
IDM Solutions developed a design methodology which takes the designer out-of-the-loop and determines the optimal set of values for the design parameters which are chosen a priori in the least number of simulations possible. The methodology utilizes a genetic algorithm (GANBI) to determine the Pareto front for a given set of competing objective functions. The two competing objective functions were to minimize material damage (the aggregate of fiber and matrix damage) while maximizing the cohesive failure. These two objectives ensure the greatest survivability of the composite while ensuring the least amount of energy transfer into or through the composite due to the imparted energy of the ballistic impact.
First, eight (8) random design generations were chosen, and corresponding simulations were performed in ABAQUS. The objectives were determined from the first iteration and then the GANBI procedure was used to generate a new generation of eight (8) designs to improve the Pareto approximation. These new designs were evaluated to find another set of objectives that were aggregated with the first set to have sixteen (16) total designs to evaluate domination/non-domination to determine a new Pareto approximation. In the fourth generation (24 individual simulations), the Pareto front was approximated which provides the optimal set of designs.
Figure 5 depicts the Von Misses stress contours for the optimal design space determined by the implemented methodology for the cohesive zone displacement. The FSP is arrested using only two (2) fiber layers. The matrix and fiber material are still intact while the fibers have delaminated from the matrix material releasing the maximum amount of energy while keeping the matrix intact.
Figure 5: Von Mises Stress Contours in the Epoxy Matrix (left) and UHMWPE Fibers (right)
The approach drastically decreased the client’s computational burden on a as the Pareto front was determined in only 24 simulations (~384 hours) over the conventional build-test-build approach which would require 3 to 4 times as many simulations (~1536 hours). Furthermore, this allowed the client to decrease the time between numerical simulations and composite panel manufacturing and as a result minimized overall manufacturing material resources and cost which maximized product design efficiency and profitability.